Simulation for Printed Circuit Board Design Reliability
Webinar
Overview:
The complexity of modern printed circuit boards (PCBs) presents design reliability challenges – from electrical, thermal, and mechanical perspectives. Increasing power dissipation and decreasing board size escalate the potential for electronic system failure due to thermal and mechanical overloading of PCBs. Modeling the coupled electrical, thermal, and thermal-induced stresses that exist in a modern PCB design is key to ensuring product reliability. This webinar will review state-of-the-art simulation techniques to analyze power and signal integrity, predict thermal performance, and overcome thermal stress, opening the door to reliable PCB designs at minimal cost and time to market.
Who Should Attend: Thermal analysts, Mechanical Engineers, PCB Designers.
Speaker: David Geb
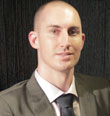
David Geb is an Application Engineer at ANSYS, focusing on electronics thermal management applications with ANSYS Icepak. His research interests include heat transfer across disparate length scales, chip-package-system thermal simulation, and thermal analysis of multi-physics applications. He has authored over 20 peer-reviewed publications in the area of heat transfer and thermal engineering. Prior to joining ANSYS he was a postdoctoral research associate at the University of Colorado, Boulder. He received his Ph.D., M.S. and B.S. degrees in Mechanical Engineering from UCLA.
Below are the audience questions asked during the live presentation.
Click on the question to view the answer.
Are the traces imported as physical solds or imported as surfaces (with assigned virtual thickness)?
The traces are imported into a PCB or package object in Icepak. The trace geometry is used in the background to quickly calculate the metal fraction distribution in the board or package substrate. The metal fraction distribution is then mapped onto the CFD mesh to determine effective properties in each CFD cell. This allows a fast and highly accurate approach to modeling the detailed heat flow paths within the PCB or package substrate.
What kind of ROM do you employ in ICEPACK? Is this method available to treat coupled physical phenomena?
The State-Space and Krylov ROM approaches are available. ROM approaches are useful in reducing the scope of LTI (Linear-Time invariant) problems. It can be used for some coupled-physical phenoma cases.
Could you perform a conduction only analysis using ANSYS mechanical?
Yes ANSYS mechanical can peform conduction only analysis. Currently though Siwave does not have automated coupling with Mechanical as it does with Icepak. So you would have to setup the heat sources manually in Mechanical – whereas the heat source profiles from Siwave are automatically transferred into Icepak. This is the current difference between Mechanical and Icepak for such conduction-only simulations.
Can trace geometries be imported from mask layout files such as GDS2 format?
Yes, but you would use an ANSYS chip-level tool to do so. ANSYS can perform chip-to package-to system thermal simulation. The first step would be to bring this into ANSYS Redhawk, generate a chip-thermal-model, and then import this into Icepak. Please contact us if you’d like more info on how to do this.
How detailed the components should be in SIwave and Icepak as the challenge always is getting a detailed model?
You can model components in full detail or using a reduced model. For example in Icepak, you can model the full geometric detail of components, use a compact conduction model, or use a 2 (or multiple) resistor network.
What is the best way to find the convection coefficient of the surfaces of the model?
The best way to find the convection coefficient of the surfaces of the model is to either (a) calculate it with a CFD simulation (h = qs/(Ts-Tair)), (b) conduct experiments or (c) refer to heat transfer coefficient tables in a text book.
How much more accurate is icepak for calculating junction temperatures of IC packages as opposed to FloTHERM (a CFD heat transfer tool) which estimates the temperature on the surface of the part?
Icepak provides highly accurate results for IC packages and their junction temperatures. Icepak employs the Fluent solver which is exhaustively verified and validated. Whether you model the package as a detailed, compact or network package object you can be confident in the accuracy of your results in Icepak.
Is ECAD more efficient than ROM in term of computing time and accuracy?
For modeling detailed ECAD geometry in thermal or structural simulations, the ECAD approach described in the presentation seems to be the way to go.
Any good reference you may recommend for learning more on thermal management?
Heat transfer textbooks are always good for fundamentals. From a simulation stand point, the ANSYS resource Library is a good starting point. Industry focused publications are good as well (electronics-cooling magazine, etc.). For specific topics Google Scholar will point to research papers.
What does ANSYS mechanical assume for material properties when computing metal fraction?
FR-4 and copper are the two materials composing the board in this example. Metal fraction refers to the volume fraction of copper in a grid cut cell. The detailed metal fraction distribution is mapped to the ANSYS Mechanical mesh for the structural simulation.
For what components on PWB we can provide vias?
Vias can be setup in the layout tool. These are then imported in to Icepak (from the ECAD file). You can setup vias how you’d like in the layout tool.
Can you give me an example about simulation switch mode power supply like Buck converter, Boost converter?
Depending on how much level of detail you want to model you can take different approaches. Some of the examples in the Icepak training and tutorial guide would be good templates for this application. You could start there.
If there is natural convection is it practical to make the CFD simulation to obtain the convection coefficient?
CFD is generally a good option for obtaining natural convection coefficients. Natural convection from a surface is often assumed to have a certain heat transfer coefficient (e.g. 5-20 W/m2K) – however you should be careful, as temperature-dependent flow and particular setups can make it difficult to know upfront the heat transfer coefficient. CFD provides a more rigorous approach to determining the heat transfer coefficient for both natural and forced flow setups.
How about varying the h from low to high to qualitatively determine the importance of ignoring a conjugate heat transfer simulation - please comment.
You can vary the h from low to high parametrically. This is a good approach to see if conjugate effects need to be considered. In some cases, temperatures in the solid can be uniform. Thank you for you feedback. Please feel free to follow up.
Can we import ECAD data into ANSYS mechanical directily and perform the analysis in ANASYS mechanical and not in ICEPAK?
Yes, you can import ECAD to ANSYS Mechanical. Currently though Siwave does not have automated coupling with Mechanical as it does with Icepak. So you would have to setup the heat sources manually in Mechanical – whereas the heat source profiles from Siwave are automatically transferred into Icepak.
Where can I use multiphysics based PWB tool?
You can use Siwave, Icepak and Mechanical for multiphysics simulation of a PCB.
What is the mesh number and typical computational resource needed for such detailed PCB simulation?
Mesh size can vary depending on user choice, whether you perform a conduction-only model, or whether you perform a full CFD model. For the example shown, performing a full CFD simulation, the mesh size was ~1.5million. If we had done conduction-only analysis the mesh size would be ~100,000 cells – much less. If high accuracy is not required you can coarsen the mesh accordingly, to get an even smaller mesh. The Icepak simulation on 4 cores, and mesh size of ~1.5million, in the example shown took around ~20min to converge. The DCIR drop took around ~5min on the same number of cores. Overall, for the multiphysics simulations performed in the example, including the multiple iterations between Icepak and SIwave (and the thermal-structural simulation), it took around 2 hours of computational time (distributed on 4 cores).